Types of Temperature Sensors For Data Centers
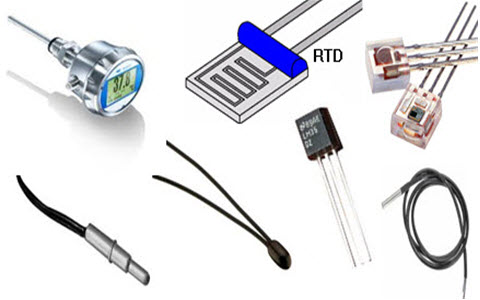
Sensors help you keep track of important environmental parameters in your data center. Typically data centers have multiple sensors installed. Temperature, humidity, power, water leak, and more. In this article, we will take a closer look at the different types of temperature sensors and their use in the data center.
A change in the data center’s temperature can cause downtime due to overheating. Downtime costs so too do the repair or replacement of the affected equipment. With proper monitoring equipment, you can quickly discover and correct problems with ambient temperature.
Selecting the right temperature monitoring system can be challenging. With so much at risk, you can’t afford to adopt a trial-and-error method. To create a safe and consistent climate in your data center, measure numerous elements and analyze the top ambient temperature monitoring systems. Depending on your data center, you may wish to consider thermal mapping each cabinet with multiple sensors on a single rack.
What Sensors Should I Use?
- Temperature
The temperature has a big impact on servers. To keep them operating properly, you must keep them within a specified operating range. Depending on the size of your data center, the age of your equipment this range can vary. Ambient temperature sensors indicate overheating, allowing you to save downtime.
- Humidity
In the data center, humidity is almost as critical as temperature. Electrostatic discharge can occur if the humidity is too low. Too high and condensation can occur. Relative humidity sensors notify you when humidity levels exceed the set range, allowing you to alter humidity levels before problems arise.
- Airflow
If your data center has poor air circulation, your equipment can suffer. Servers that take in hot, stagnant air can’t cool efficiently. Airflow sensors enable you to map out and track your data center’s airflow and design a more stable ambient environment. For example, if the air is hot under racks, consider implementing an air delivery system to push that air up.
Sensor Placement
When deploying rack-level sensors, start by focusing on hot zones. Because heat rises, sensors should be placed at the tops of your racks. Place sensors at the top, bottom, and middle of your server racks to get a complete view of airflow in your data center. Placing sensors at both the front and rear of the rack allows you to monitor the incoming and exhaust air temperatures and calculate delta T (∆T).
In-room sensors should be placed near air conditioning equipment. This allows you to pinpoint problems with specific air conditioning systems; otherwise, your sensors won’t be able to detect a problem since the other units will work overtime to compensate. Consider which places make the most sense for placement based on the configuration of your data center.
Types of Temperature Sensors
Temperature sensors are used on a daily basis for building temperature management, water temperature regulation, and refrigerator control. Temperature sensors are also used in consumer, medical, and industrial electronics.
Temperature sensing requirements may vary by application. What’s being measured (air, mass, or liquid), where it’s being measured (inside or outdoors), and the temperature range being monitored are all factors to consider. The thermocouples, resistance temperature detectors (RTD), thermistors, and semiconductor-based integrated circuits are the four most popular types of temperature sensors in modern electronics (IC).
Thermocouples
The most common type of temperature sensor is the thermocouple. They are utilized in a variety of industries, including manufacturing, automotive, and consumer goods. Thermocouples are self-powered, do not require stimulation, and respond quickly. They can function at a wide range of temperatures.
Thermocouples are manufactured by connecting two metal wires that are not the same. There is a Seebeck Effect as a result of this. The Seebeck Effect occurs when a temperature difference between two different conductors results in a voltage difference between the two substances. This voltage difference may be measured and used to compute the temperature.
Thermocouples come in a number of shapes and sizes and are constructed from a variety of materials, allowing for a wide range of temperature ranges and sensitivities. The various categories are distinguished by the letters assigned to them. The K-type is the most often utilized.
The fact that thermocouples have a limited output voltage, which necessitates accurate amplification, as well as their sensitivity to external noise via long cables and cold junctions, makes temperature measurement difficult. The thermocouple wires contact the copper traces of the signal circuitry at a cold junction. This results in a second Seebeck Effect, which must be adjusted using a technique known as cold junction compensation.
RTD (Resistance Temperature Detector)
The resistance of any metal changes as the temperature changes. RTD temperature sensors are based on this differential in resistance. A resistor with well-defined resistance vs. temperature properties is known as an RTD. The most popular and accurate material used to create RTD is platinum.
PRTD is another name for platinum RTD. At 0°C, they are frequently available with resistances of 100 and 1000. They’re known as the PT100 and PT1000, respectively.
Platinum RTD is employed because they have a nearly linear temperature response, is stable and accurate, produces reproducible responses, and has a broad temperature range. Because of their accuracy and reproducibility, RTD is frequently utilized in precision applications.
RTD elements usually have higher thermal mass, and therefore respond slower to changes in temperature than thermocouples. Signal conditioning is important in RTD. They also require an excitation current to flow through the RTD. If this current is known, the resistance can be calculated.
Configurations include two, three, and four-wire options. The two-wire option is useful when the lead length is short enough that resistance doesn’t significantly affect measurement accuracy. A three-wire adds an RTD probe that carries the excitation current. This provides a way to cancel wire resistance. Four-wire is the most accurate, as separate force and sense lead eliminates the effect of wire resistance.
Thermistors
Temperature variations induce quantifiable resistance changes in thermocouples, which are comparable to RTD. Thermistors are often constructed of a polymer or ceramic. Thermistors are often less expensive than RTD, but they are also less precise. The majority of thermistors come in two-wire layouts.
The most often used thermistor for temperature measurement is the Negative Temperature Coefficient (NTC) thermistor. The resistance of an NTC thermistor reduces as the temperature rises. The temperature resistance of thermocouples is non-linear. To appropriately understand the data, this necessitates a large modification.
Semiconductor Based ICS
There are two types of temperature sensor IC based on semiconductors: local temperature sensors and distant digital types of temperature sensors. Local temperature sensors are integrated circuits that use the physical attributes of a transistor to monitor the temperature of their own die. The temperature of an external transistor is measured using remote digital temperature sensors.
Analog or digital outputs are available for local temperature sensors. Digital outputs come in a variety of forms, including I2C, SMBus, 1-Wire, and Serial Peripheral Interface (SPI). Analog outputs can be either voltage or current. The temperature of printed circuit boards or the ambient air surrounding them is sensed using local temperature sensors.
Remote digital temperature sensors use the physical features of a transistor to function similarly to local temperature sensors. The transistor is separated from the sensor chip in this case. A bipolar sensing transistor is included in some microprocessors and FPGA to measure the target IC die temperature.
Allow Real-Time Temperature Monitoring To Speak For Itself
A minimum of six temperature sensors per rack is recommended by ASHRAE. To monitor air intake and exhaust temperatures, three will be placed in the front (at the top, middle, and bottom) and three in the back. More than six sensors per rack are commonly used in high-density facilities to construct more exact temperature and airflow models, which is highly recommended, especially for data centers operating at an ambient temperature of 80°F.
Why? Because you can’t find a hotspot if you can’t see it, to put it simply. When a safe temperature threshold is surpassed, real-time temperature monitoring connected to your data center’s network will inform selected employees through SNMP, SMS, or email.
Again, the more sensors you have, the better. It’s wonderful to know that you’ll always have access to a real-time alerting system. It’s much better if you can look at a computer-generated model driven by a slew of rack sensors and track down the source of the problem.
AKCP Temperature Sensors
Single Port Temperature and Humidity Sensor
When you need to know the temperature of a room, enclosure, or cabinet this sensor can be used. Housed in a thermally conductive metal tube it is accurate and quick to react to changes in temperature. The sensor can be easily mounted with screws, adhesive, or optional DIN rail clips making it ideal to scatter around the facility as well. Combining temperature and humidity into one sensor frees up an additional intelligent sensor port on your base unit. Thresholds can be set for low and high warning and critical parameters. The built-in graphing function of the base unit gives you a pattern of temperature or humidity trends over time.
Cabinet Analysis Sensor
The Cabinet Analysis Sensor (CAS) features a cabinet thermal map for detecting hot spots and a differential pressure sensor for analysis of airflow. Monitor up to 16 cabinets from a single IP address with the sensorProbeX+ base units. The Wireless Cabinet Analysis Sensor is also available using our Wireless Tunnel Technology.
Differential pressure sensor, check for proper pressure differential between front and rear. Ideal for hot and cold aisle containment to ensure proper airflow. AKCPro Server Rack Map View Use the CAS with dedicated rack map views on AKCPro Server. A visual representation of your cabinet, with airflow, front and rear temperatures, temperature differentials, and differential pressure.
Wireless Temperature Sensors
AKCP also offers wireless temperature sensors with a built-in calibration check. Wireless Tunnel NIST2 sensors feature 2x NIST traceable, calibrated temperature sensors in a single stainless steel tube.
Summary
Thermocouples are low-cost, long-lasting temperature sensors that can measure a wide range of temperatures. RTD is slower and requires an excitation current, and signal conditioning is required. Semiconductor-based integrated circuits are simple to implant and may be packed in incredibly small packages.
Reference Links:
https://www.electronics-tutorials.ws/io/io_3.html
https://www.digikey.ph/en/blog/types-of-temperature-sensors
https://iriss.com/articles/is-a-wireless-temperature-monitoring-system-feasible-for-critical-electrical-asset-reliability/